Smart Factory is the New Age Innovation in the Automotive Industry
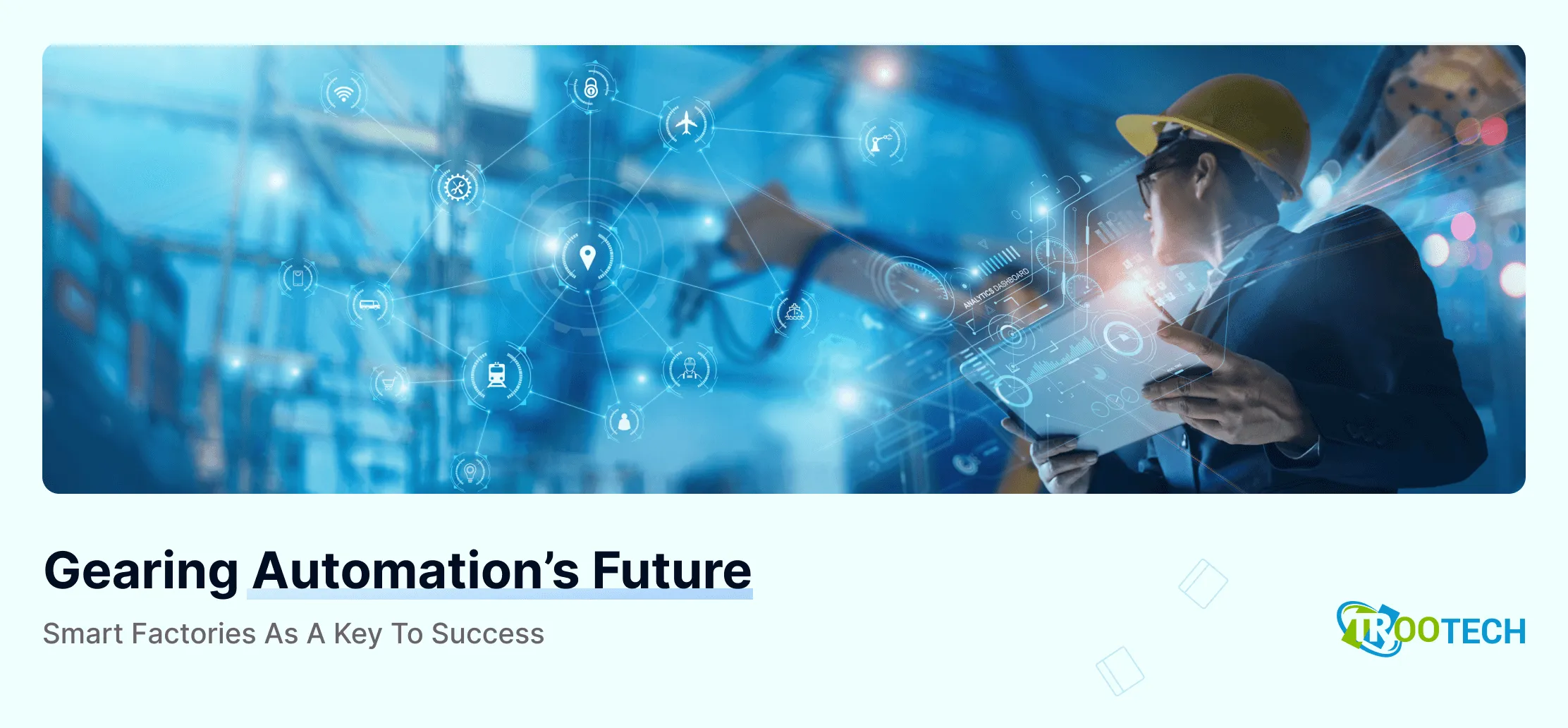
Smart industrial systems’ debut to contemporary businesses
Connectivity is not a novel concept in the process of manufacturing. However, recent events like Industry 4.0, the fourth industrial revolution, and the fusion of the physical and the digital worlds, combining information technology (IT) and operations technology (OT), have made supply chain transformation more and more feasible.
The cornerstone for how businesses thrive in the future may be set by the transition from linear, incremental supply chain operations to an accessible, linked system of supply operations defined as the virtual supply network.
Moreover, in order to actualize the digital supply network, manufacturers will likely need to unlock a number of functionalities, including end-to-end, comprehensive, and integrated connectivity throughout the complete value chain and horizontal integration via a plethora of operational databases that influence the organization. The transition from more conventional automation to a fully networked and dynamic system is represented by the smart factory.
How has the expansion of business made room for smart industrial systems?
OEMs and suppliers have lately discovered that their existing production capabilities are not sufficiently effective. As per them, the current production systems are unadaptable and can’t effectively produce the next generation of automobiles as the sophistication of the auto manufacturing industry increases.
Industry-leading suppliers and manufacturers are using digitization and automation to convert their facilities into intelligent manufacturing environments.
In order to move towards smart manufacturing technology systems, businesses began utilizing the IIoT, sensors, cloud technology, and big data analytics, which we will briefly discuss in the blog’s following subsections. We will learn that such phases will bring significant improvement in workers’ performance by providing for instant bottleneck resolution, operational efficiencies performance, improved cooperation, and proactive maintenance.
Car manufacturers and suppliers may upgrade accumulated capital, processes, and resources with these smart manufacturing technology solutions, enhancing present production capabilities with versatility, standardization, and cybersecurity.
The seasoned timeline of smart manufacturing in businesses
1) The First Industrial Revolution (Industry 1.0):
The First Industrial Revolution was a period of economic change that labeled the transition from an agrarian and handicraft-based economy to one dominated by machinery. It had a substantial impact on sectors like mineral extraction, textile materials, glass, and agriculture.
2) The Second Industrial Revolution (Industry 2.0):
This phase saw substantial economic expansion and a rise in productivity, but it also resulted in a significant spike in unemployment because many manufacturing workers were replaced by computers.
3) The Third Industrial Revolution (Industry 3.0):
The core of this stage, also referred to as Industry 3.0 or the Digital Revolution, is the mass production and broad adoption of digital logic, MOS transistors, programmable chips, and technologies inferred from these, such as computer system, microcontrollers, virtual cellular telephones, and the Internet.
4) The Fourth Industrial Revolution (Industry 4.0):
This stage is the fusion of advanced digital technologies with tangible assets, including the Internet of Things (IoT), Artificial Intelligence (AI), robotic systems, drones, autonomous cars, 3D printing, cloud computing, and others. These innovations are intertwined and have the ability to communicate, analyze, and act.
Understanding the smart factory activators
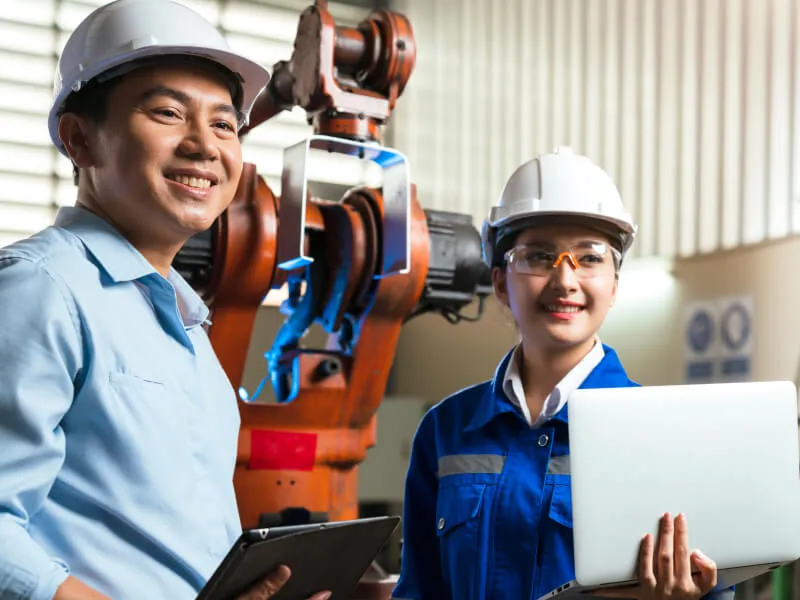
Digital technologies are used in “smart” factories to significantly increase output, quality, services, and adaptability. The smart factory is enabled by three essential digital technologies:
– Connectivity, such as using the Industrial IoT to collect information from both old and new sensors
– Intelligent Automation, such as cutting-edge robotic systems, computer vision, distributed control, and drones.
– Cloud-scale data management and analytics: Integrating predictive modeling and AI, for instance, is a paradigm of cloud-scale data management and analysis.
Along with supporting end-to-end virtual continuity from design to operations, these technological advances will also facilitate IT-OT convergence (digital twin). A closed-loop, data-driven enhancement of end-to-end processes is the key feature of a smart factory.
The eventual aim of advanced statistics is to achieve self-optimizing operations, primarily utilized to support decision-making. This is where the factory continuously adjusts to shifts in supply, demand, and process.
Does your business need an IT specialist team?
Smart factories integrated with intelligent technologies
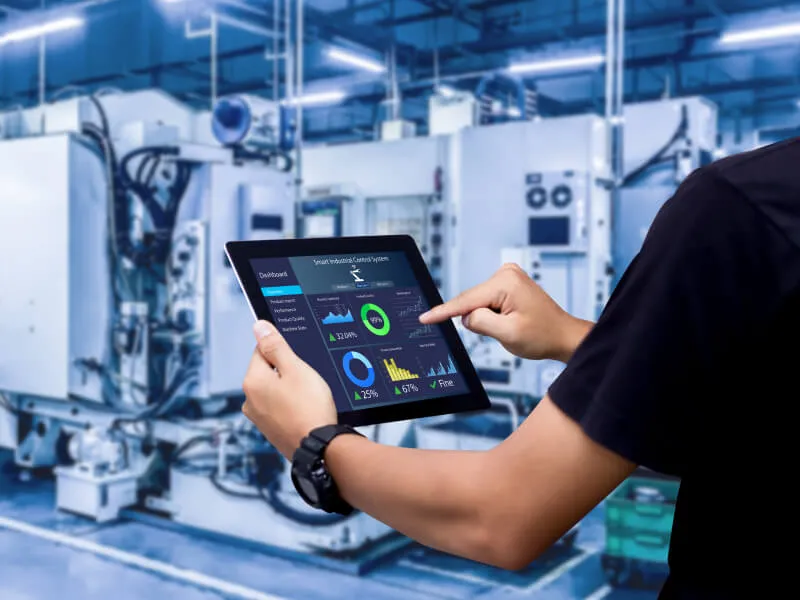
Industries 4.0 (IIoT)
In order to enable the transmission and utilization of information between individuals and machines the term “Industrial IoT” describes a system of interconnected devices, automated systems, and procedures that are linked by data communications networks. These instruments generally involve sensors that gather useful data for storage in the cloud or an offline database. The factory floor manufacturing processes can be tracked and improved using this data.
Cloud Computing
In comparison to conventional on-premise options, cloud computing enables companies to store, process, and exchange information with increased flexibility and at a cheaper cost. Since cloud computing enables massive amounts of information to be transmitted at breakneck speeds, linked machines and devices on the factory floor become more powerful.
Additive Printing:
Additive printing, also referred to as 3D printing, enables intelligent automation for on-demand manufacturing in smart manufacturing technology. This is especially important when a supply chain is suddenly disrupted or when there is a spike in product demand. Digital inventories, however, can significantly reduce uncertainty and wastage even when things are going according to plan by enabling just-in-time manufacturing.
Massive Data Analysis
Data collection over time can reveal information about the effectiveness of the manufacturing process, important parameters to monitor, and underperforming systems. Big Data has a high level of precision for predictive quality control and can identify error patterns. A brief glance at current market trends indicates that most businesses have made little headway in their road towards digitizing the factory floor, despite the reality that smart manufacturing technology has recently gained popularity in manufacturing circles.
Digital Twins:
A machine or system’s digital twin is a precise, virtual reproduction of it. It permits the most innovations and creativity while posing the fewest operational risks. Without ever running the risk of harming people or wasting valuable resources in the real world, a digital twin can be stretched to its absolute limits, customized in various virtual ways, or evaluated to see if it works with a current framework.
Sensors
At various phases of the manufacturing process, sensors linked to tools and machinery gather and produce insights that can be used to take appropriate action. For instance, the environment in a lab can be tracked and detected by temperature sensors in a cleanroom, and the data can be shared through an IoT gateway. Using AI, this information can self-correct to address any anomalies or abnormalities or notify team members for a review.
AR/VR Applications:
AR and VR applications in the smart factory include “being able to link together climate factors, stock levels, process state, assembly failure data, utilization, and throughput indicators in a context-dependent approach (where you look or walk),” according to Assembly Magazine in 2019. In order to provide consumers with a clear understanding of the status of the factory, this immersive sensory experience allows them to supplement their natural sensations with actual statistics from any time or location.
Blockchain:
Interestingly, security solutions are developing at the same rate as smart industrial technology. From establishing “smart contracts” with suppliers to monitoring the authenticity of items and handling them throughout the supply chain trip, blockchain has various uses in the supply chain. Blockchain is particularly helpful in managing access to connected assets and machines throughout the company in smart factories, ensuring the system’s security and the veracity of the data those devices hold.
Modern ERP systems and in-memory databases serve as the “brains” of Industry 4.0, smart factories, and intelligent supply chain solutions. To keep up with the sophisticated data management and analytics features required to operate smart factories and contemporary supply chains, legacy, disk-based databases are sometimes stretched far beyond their breaking point.
Numerous manufacturers have invested millions of dollars in Industry 4.0 and Internet of Things programmes, yet they have seen no tangible benefits as a result. Let’s examine this with some examples to see why it is the case.
Want to get started with an expert-backed process?
Top 3 benefits that smart factory lends to automotive industries

The supply chain procedures and systems utilized by numerous firms haven’t evolved much in generations. But supply chain executives require solutions that can deliver quantifiable and substantial benefits – and can offer them swiftly – at a time when consumer demands and economic uncertainties are both at an all-time peak. There is an opportunity for significant business benefits for businesses that engage in digitalization and smart manufacturing technology, including
#1 Productive output and efficiency:
Throughout history, manufacturing has mostly revolved around reacting — looking at an incident or a pattern that has already occurred and then attempting to guide the company in a different way after the facts.
In order to eliminate the requirement for reactive activities and shift supply chain management toward a more adaptable and proactive phase, smart manufacturing technology was developed. Big Data analysis and predictive analytics enable the identification and implementation of efficient procedures.
Among the operational advantages that intelligent factories offer are enhanced time-to-market, precise sales forecasting, and just-in-time inventory control. The employees in smart factories are able to simplify their tasks with the help of digital insights, which raises the operation’s productivity as a whole.
Deloitte claims that after investing in smart factory projects, “Companies report up to 12% increases in areas including manufacturing production, factory utilization, and labor productivity.” Furthermore, smart factories will probably outperform conventional manufacturing by 2030 thanks to a 30% higher net labor productivity.
#2 Sustainability and safety:
Customers are increasingly willing to pay a little bit more for goods they are confident were sourced and produced in an ethical and environmentally conscious manner. Businesses may now more easily than ever recognize and implement possibilities for greener, safer, and socially conscious manufacturing methods. This is because of the development of modern smart industrial technologies.
Smart factory managers can employ technological advancements like Blockchain and RFID sensors to guarantee the unquestionable traceability and quality assurance of all materials and supplies, regardless of where they originate from the supply chain. And pretty close to home, according to the International Society of Automation, three out of the top five reasons for workplace fatalities can be decreased or completely eliminated with the aid of robots and other automated devices.
#3 Quality of the product and consumer experience:
Conventional manufacturers often struggled to make sure their instructions were correctly understood and carried out by the lowest tier suppliers and manufacturers in their supply chains, much like the children’s telephone game. All stages of the manufacturing process receive real-time data and recommendations in the smart factory thanks to cloud connectivity and end-to-end visibility.
Products can be quickly customized and updated to reflect changing trends, keeping them close in line with consumer preferences. Sophisticated system data analysis immediately identifies flaws or potential improvement opportunities. As a result, the market is more dynamic, the product gets better evaluations, and there are very few pricey returns or recalls.
A couple of the finest smart factory implementation case studies
Greenfield smart factory by Audi
Technological innovations and a burgeoning variety of vehicle variations are becoming more and more necessary due to increased production and regulatory complexity, fluctuating market demands, and shifting consumer expectations.
This indicates that the conventional production line with set times is losing efficiency. The growing percentage of model derivatives and variants adds to the process’s sophistication and necessitates the integration of additional routines into its inflexible, sequential structure.
In order to meet these obstacles, Audi is coming up with a brand-new idea it calls “modular assembly.” To construct the next-generation Audi Q5 for the global market, Audi launched a 400-acre, USD1.3 billion smart facility in Mexico as part of this.
The plant will create cars for customers that are “tailored to their specific desires” and has a production capacity of 150,000 of these high-end SUVs annually. On the entire continent of North America, it is regarded as one of the most cutting-edge factories.
A list of innovative technologies used in the factory includes:
– Virtual assembly technology
– Autonomous ground vehicle
– Driverless floor conveyor
– Remote maintenance portal
– Metal 3D printing center
– Collaborative robots
– Drones
Audi has never before operated a plant entirely digitally, i.e., through computer simulation, with industrial planning carried out using cutting-edge technologies. A supplier park is located close to the factory. This just-in-sequence (JIS) supplier parking next to the assembly line enables prompt component delivery.
Benefits provided by the Greenfield smart factory:
The smart factory at Audi was set up 30% quicker than usual. The entire product lifecycle chain was also optimized in the factory. It uses automated quality control, RFID, centralized production management, and smart logistics.
Audi is able to organize the manufacturing and the supply chain with significant flexibility because of these capabilities, which results in incredibly high productivity and effectiveness levels. The factory also uses resources wisely.
The factory will be devoid of effluent thanks to modern water treatment techniques and the use of technology in the paint shop. Additionally, the machinery it makes will drastically utilize less water, gas, and energy.
Factory 56 at Mercedes Benz
The modern digital facility from Mercedes-Benz, “Factory 56,” covers 220,000 square meters and will be utilized to make a variety of vehicles, spanning elegance, hybrid, fully electric, and self-driving.
Key elements that are included in Factory 56:
- Many places use “TecLines” in place of the conventional assembly line, which uses autonomous transport systems (DTS) to carry built-in programmes from section to section. DTS allows for the expansion of single assembly units without affecting the property’s structural integrity.
- The Internet of Things (IoT), which is dependent on a mobile phone network, is employed in assembly lines and materials handling technologies. The assembly hall is completely paperless, with personnel using panels and individual digital assistants. A prototype application is scheduled to test the usage of 5G in assembly.
- Components and pieces required for assembly are automatically selected by smart picking systems from pick zones. Fully autonomous shopping carts are subsequently used to transport these components to the assembly sites. There are about 300 driverless transportation systems in use.
Utilizing analytics technology, acquired data is evaluated, and the results are then used to enhance current procedures. This aids in predictive maintenance and prevents plant faults.
Advantages to Mercedes Benz by Factory 56
Assembly is made more effective and flexible by integrating a production line with “TecLines,” allowing production to be altered without interfering with ongoing operations. This method lengthens operation times while improving quality.
Early supply chain inconsistency detection via tracking and tracing allows for quick response times. Additionally, the plant strives to provide CO2-neutral energy. A photovoltaic ( pv ) system on the industrial roof supplies the hall with green electricity that is self-generated.
Statistics that speak for sustainable smart factories and manufacturing for Automotives
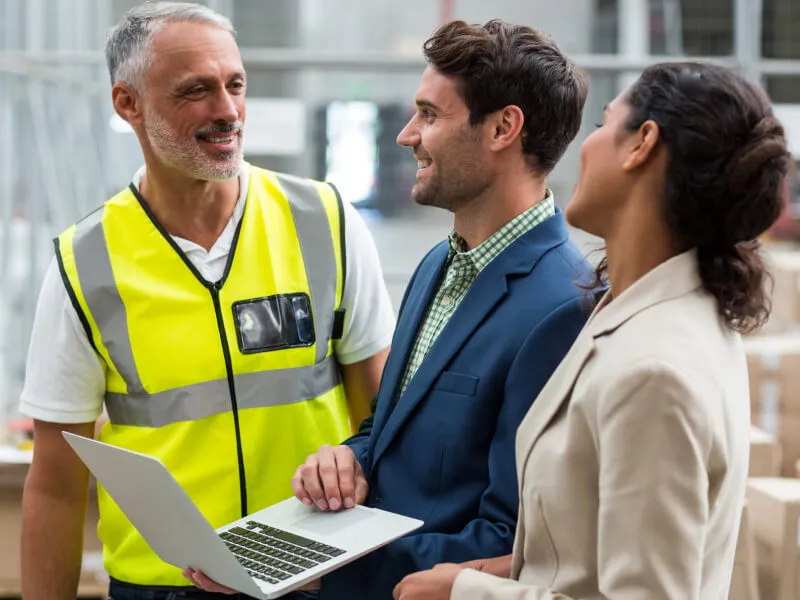
The demand for smart factories in the automotive industry is substantial. And considering the large reward on the table—the sector hopes to obtain multibillion-dollar gains from smart factories—that thirst is justifiable. Here are a few statistics that speak in length about how smart factories would be the mainstream of automotive manufacturing in the near future –
- 10% more as compared to 18 months before, automotive companies are making good progress on their roadmap for smart factories.
- In the last 18 to 24 months, three out of ten auto manufacturers have undergone a smart transformation.
- In the next five years, the automotive industry plans to transform 44% of its facilities into smart factories.
- The automobile industry intends to expand investment in smart factories by more than 60%.
- Four out of every five auto companies favor building new facilities, given the scope of smart factories.
- Smart factories are projected to boost the car sector to make up USD167 billion.
While certain OEMs and a small percentage of the leading providers have been able to advance in their smart factory journeys and experience meaningful benefits, the overwhelming majority of them still need to address a number of issues before they can grow and win the smart factory prize.
Both OEMs and suppliers will need to move quickly on a number of topics, such as strategy, integrated systems solutions, IT-OT convergence, and a talent relaunch, in order to meet their objectives.